Mariani Nut Company Tour
- christinayliu
- May 25, 2023
- 4 min read
March 2, 2023
It was a chilly, but sunny, winter day. We all excitedly piled into our cars, and alongside us is our Biodesign instructor, Christina Cogdell. Our destination was Winters, California, a small but beautiful town in central California, to visit the Mariani Nut Company.

Founded by two cousins in 1972, the family-owned Mariani Nut Company is considered "one of the largest, privately-held, walnut and almond processors in the world" (Mariani Nut Company), supplying their almonds and walnuts to nearly 70-80% of the international market, with the rest being consumed in the States.
Mariani Farms is a farmer, seller, and distributor of nuts, with the company and farm conducting separate business operations. The farmers grow and harvest the nuts, which are then transported to the company to be branded, packaged, and shipped out to stores. Furthermore, Mariani doesn’t exclusively sell their products under their name. They also act as a supplier to major corporate brands, like those in the food service industry making cereal and ice cream, as well as major brands like Kirkland Signature, to just name a few.
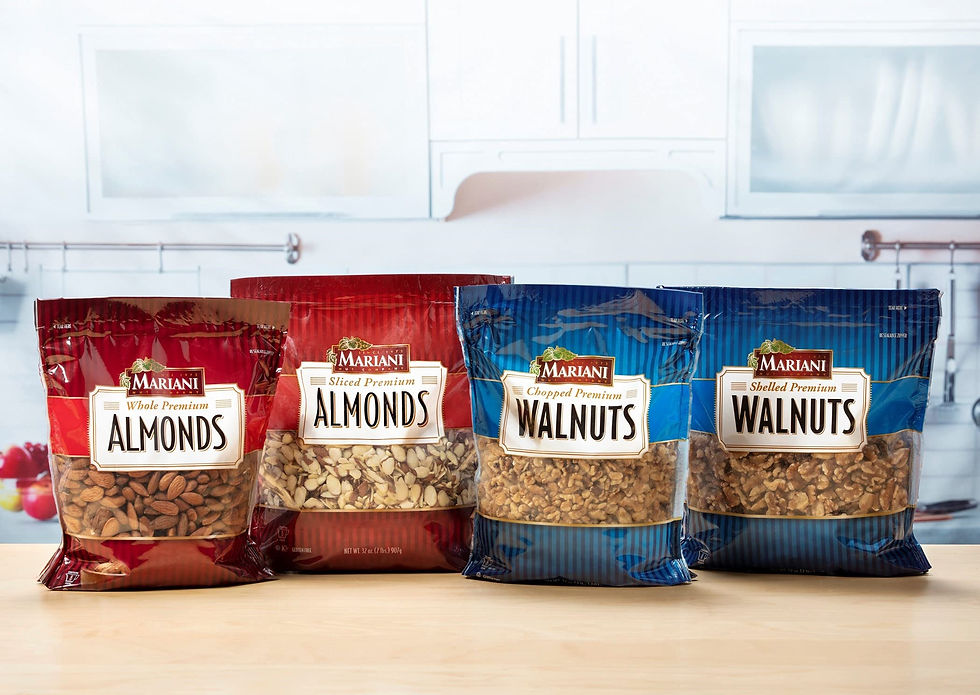
Here's the Gang!

The team with our wonderful instructor, Christina Cogdell
What's the Issue?
With Mariani Nut Company working on such a large-scale operation, the agricultural waste they leave behind is just as big. Knowing this, we were excited to tell our amazing Mariani Nut Company host and tour guide, John Rodriguez, about our innovative solution to reducing walnut shell waste.
Although we did not have any physical prototypes to show to John, we were able to share some samples of various starches and materials that were used to bond fabric waste together. Such materials ranged from ranging from potato starch, corn starch, and even gelatin! Each sample gave a different texture, flexibility, and strength. At this point, we decided that the various starches would best suit our ideal paperboard.
After hearing our idea and feeling the various samples, John was just as excited as us!
What Did We Learn?
We learned a lot. None of us were very familiar with the nut or packaging industry, but everything we did learn established a foundational understanding to the problem we wanted to solve.
Our tour started at the silos, which towered over us as we approached them from the parking lot. According to John, each silo stores about 1 million pounds of walnuts, which is the equivalent of 500 tons. The walnuts are all stored in their shells within the silos due to the shell's ability to preserve their freshness for up to three months!
Just a taste of what we encountered in the silos
We then asked about the process behind harvesting the walnuts, and we learned the steps of the entire process from planting the walnut trees to shipping them out internationally.

Nut trees are planted around August
Throughout the year, the trees bloom, flowers, and then the walnut fruits start to grow
Walnut hulls grow, but generally slack off near harvesting season
Growers harvest these fruit, or in this case, the walnut in its shell, into large containers
Walnuts are washed down with an electric powered water pressure hose
Then, they're treated by heat (also powered by electricity)
Once dry, walnuts are either stored in whole shells and placed in the silo or are sent to the facility to be shelled
Shelled nuts go through the machinery to be separated, but also have manual aspects to the process too
Nuts are individually packaged through a mix of auto / machine or manually
Packages of nuts are put into boxes, either to be stored or shipped out
Some interesting facts we found were how walnuts were harvested because walnut trees don’t bloom flowers, the hulls come apart when harvest time comes, and are still discarded in a mulch later on. After the whole nuts are cleaned and water washed, they are placed in open containers still wet, but the heat produced at the bottom comes upward and dries the walnuts. The drying process can take 12-36 hours to dry with 6% to 8% left to prevent the walnuts from getting brittle and breaking. Then, they are placed into silos.
This process takes up a lot of energy and produces 6.72 million pounds of walnut shells of the 12.5 million pounds of walnuts harvested.
More About the Issue

During the tour, we learned that on top of producing and supplying nuts, they also create their own packaging alongside packaging for companies they have partnerships with but not their own boxes. This means that although they have their own packaging supply they need to outsource for their boxes. Mariani Farms have 160 different variations of designs for their brand, meaning they have 160 different variations of boxes they need to be supplied. These boxes are all designed differently with the 3rd party being able to print the cardboard boxes with the Mariani label.
This information was great to know because we learned that different strengths of cardboard are utilized for different amounts of walnuts that are shipped. Each box is specific to the client's wants, even if they want their walnuts shipped in thinner cardboard that can easily break under pressure, due to the high shipping fees.

We see this as a great opportunity to utilize agricultural waste, specifically walnut shells to eliminate the massive walnut shell waste that is generated from domestic and global markets through our product, Walbox. Currently, walnuts are being burned to create an alternative fuel, which is extremely inefficient. The product being produced from agricultural waste will hopefully be biodegradable so that a circular loop can be created in the life cycle. This is an important factor because our product will not only be utilizing the vast amount of waste but also creating a product that can be biodegraded safely, though this also depends on the additional materials used during the creation process of Walbox. The amount of cardboard packaging waste from food storage and shipping is 850 million tons. Ideally, our solution can prevent and dissuade our users from contributing to cardboard waste in landfills and offset a large amount of energy and chemical input to create new cardboard.
Takeaways for our Product
From our tour at Mariani Nut Company, we were able to further understand the sheer scale of our issue, see the current industry standards and practices in place for our target audience, and discuss with real-life people involved.
This experience has only become fuel to our inspiration and motivations to continue to achieve this product!
Us as a human scale to showcase the number of boxes & walnuts in the facility!
Comments